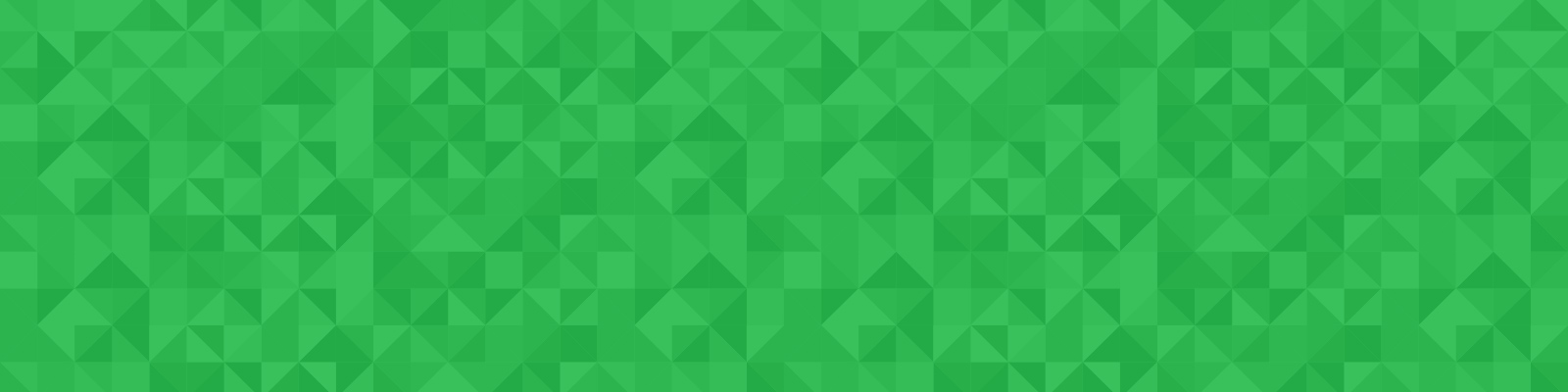
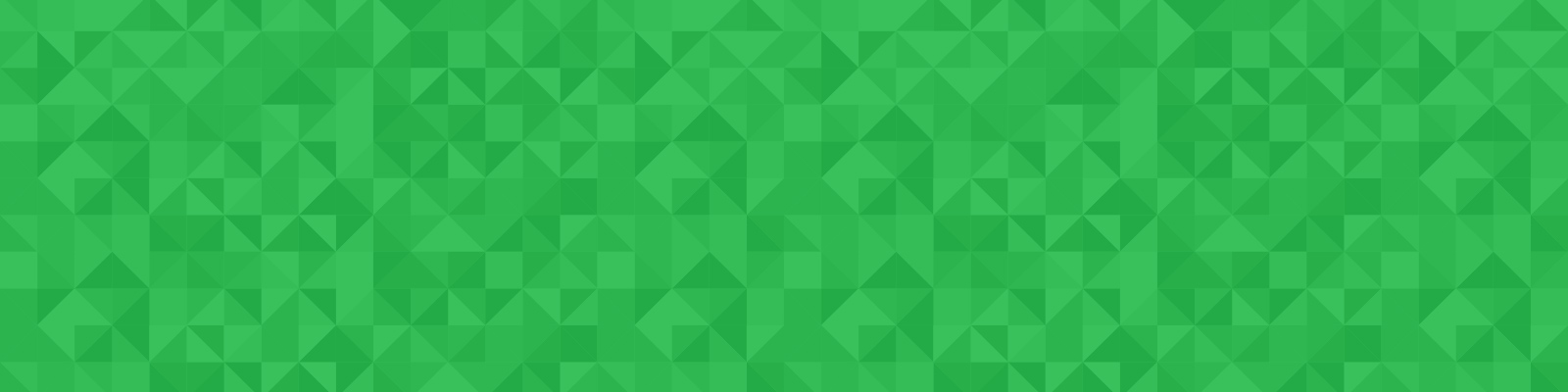
Molding machine business
-
standard_machine
Standard Injection Molding Machine
-
special_purpose_machine
Special Purpose Injection Molding Machine
-
magnesium_injection_molding_machine
Magnesium injection molding machine
-
multilayer_blow_molding_machine
Multilayer Blow Molding Machine
-
add-on_device
Add-on Device
-
iot
IoT
Products Menu
-
standard_machine
Standard Injection Molding Machine
-
special_purpose_machine
Special Purpose Injection Molding Machine
-
magnesium_injection_molding_machine
Magnesium injection molding machine
-
multilayer_blow_molding_machine
Multilayer Blow Molding Machine
-
add-on_device
Add-on Device
-
iot
IoT
We manufacture, sell, and provide maintenance services for plastic molding machines (Plastic Injection Molding Machine, Multilayer Blow Molding Machine, etc.) and Magnesium injection molding machine.
Plastic injection molding machines: produce a variety of plastic products from automobile bumpers to connectors for electronic devices.
Magnesium injection molding machines: Mold magnesium alloys as precisely as plastic.
Products & Services
Standard Injection Molding Machine
-
$事業部門名$
$製品名$
$製品概要テキスト$$製品概要テキスト$$製品概要テキスト$$製品概要テキスト$$製品概要テキスト$$製品概要テキスト$
$タグ$
$タグ$$タグ$$タグ$
$タグ$$タグ$$タグ$
-
$事業部門名$
$製品名$
$製品概要テキスト$$製品概要テキスト$$製品概要テキスト$$製品概要テキスト$$製品概要テキスト$$製品概要テキスト$
$タグ$
$タグ$$タグ$$タグ$
-
$事業部門名$
$製品名$
$製品概要テキスト$$製品概要テキスト$$製品概要テキスト$$製品概要テキスト$$製品概要テキスト$$製品概要テキスト$
$タグ$
$タグ$$タグ$$タグ$
Special Purpose Injection Molding Machine
-
$事業部門名$
$製品名$
$製品概要テキスト$$製品概要テキスト$$製品概要テキスト$$製品概要テキスト$$製品概要テキスト$$製品概要テキスト$
$タグ$
$タグ$$タグ$$タグ$
$タグ$$タグ$$タグ$
-
$事業部門名$
$製品名$
$製品概要テキスト$$製品概要テキスト$$製品概要テキスト$$製品概要テキスト$$製品概要テキスト$$製品概要テキスト$
$タグ$
$タグ$$タグ$$タグ$
-
$事業部門名$
$製品名$
$製品概要テキスト$$製品概要テキスト$$製品概要テキスト$$製品概要テキスト$$製品概要テキスト$$製品概要テキスト$
$タグ$
$タグ$$タグ$$タグ$
Magnesium injection molding machine
-
$事業部門名$
$製品名$
$製品概要テキスト$$製品概要テキスト$$製品概要テキスト$$製品概要テキスト$$製品概要テキスト$$製品概要テキスト$
$タグ$
$タグ$$タグ$$タグ$
$タグ$$タグ$$タグ$
-
$事業部門名$
$製品名$
$製品概要テキスト$$製品概要テキスト$$製品概要テキスト$$製品概要テキスト$$製品概要テキスト$$製品概要テキスト$
$タグ$
$タグ$$タグ$$タグ$
-
$事業部門名$
$製品名$
$製品概要テキスト$$製品概要テキスト$$製品概要テキスト$$製品概要テキスト$$製品概要テキスト$$製品概要テキスト$
$タグ$
$タグ$$タグ$$タグ$
Multilayer Blow Molding Machine
-
$事業部門名$
$製品名$
$製品概要テキスト$$製品概要テキスト$$製品概要テキスト$$製品概要テキスト$$製品概要テキスト$$製品概要テキスト$
$タグ$
$タグ$$タグ$$タグ$
$タグ$$タグ$$タグ$
-
$事業部門名$
$製品名$
$製品概要テキスト$$製品概要テキスト$$製品概要テキスト$$製品概要テキスト$$製品概要テキスト$$製品概要テキスト$
$タグ$
$タグ$$タグ$$タグ$
-
$事業部門名$
$製品名$
$製品概要テキスト$$製品概要テキスト$$製品概要テキスト$$製品概要テキスト$$製品概要テキスト$$製品概要テキスト$
$タグ$
$タグ$$タグ$$タグ$
Add-on Device
-
$事業部門名$
$製品名$
$製品概要テキスト$$製品概要テキスト$$製品概要テキスト$$製品概要テキスト$$製品概要テキスト$$製品概要テキスト$
$タグ$
$タグ$$タグ$$タグ$
$タグ$$タグ$$タグ$
-
$事業部門名$
$製品名$
$製品概要テキスト$$製品概要テキスト$$製品概要テキスト$$製品概要テキスト$$製品概要テキスト$$製品概要テキスト$
$タグ$
$タグ$$タグ$$タグ$
-
$事業部門名$
$製品名$
$製品概要テキスト$$製品概要テキスト$$製品概要テキスト$$製品概要テキスト$$製品概要テキスト$$製品概要テキスト$
$タグ$
$タグ$$タグ$$タグ$
IoT
-
$事業部門名$
$製品名$
$製品概要テキスト$$製品概要テキスト$$製品概要テキスト$$製品概要テキスト$$製品概要テキスト$$製品概要テキスト$
$タグ$
$タグ$$タグ$$タグ$
$タグ$$タグ$$タグ$
-
$事業部門名$
$製品名$
$製品概要テキスト$$製品概要テキスト$$製品概要テキスト$$製品概要テキスト$$製品概要テキスト$$製品概要テキスト$
$タグ$
$タグ$$タグ$$タグ$
-
$事業部門名$
$製品名$
$製品概要テキスト$$製品概要テキスト$$製品概要テキスト$$製品概要テキスト$$製品概要テキスト$$製品概要テキスト$
$タグ$
$タグ$$タグ$$タグ$